TPM
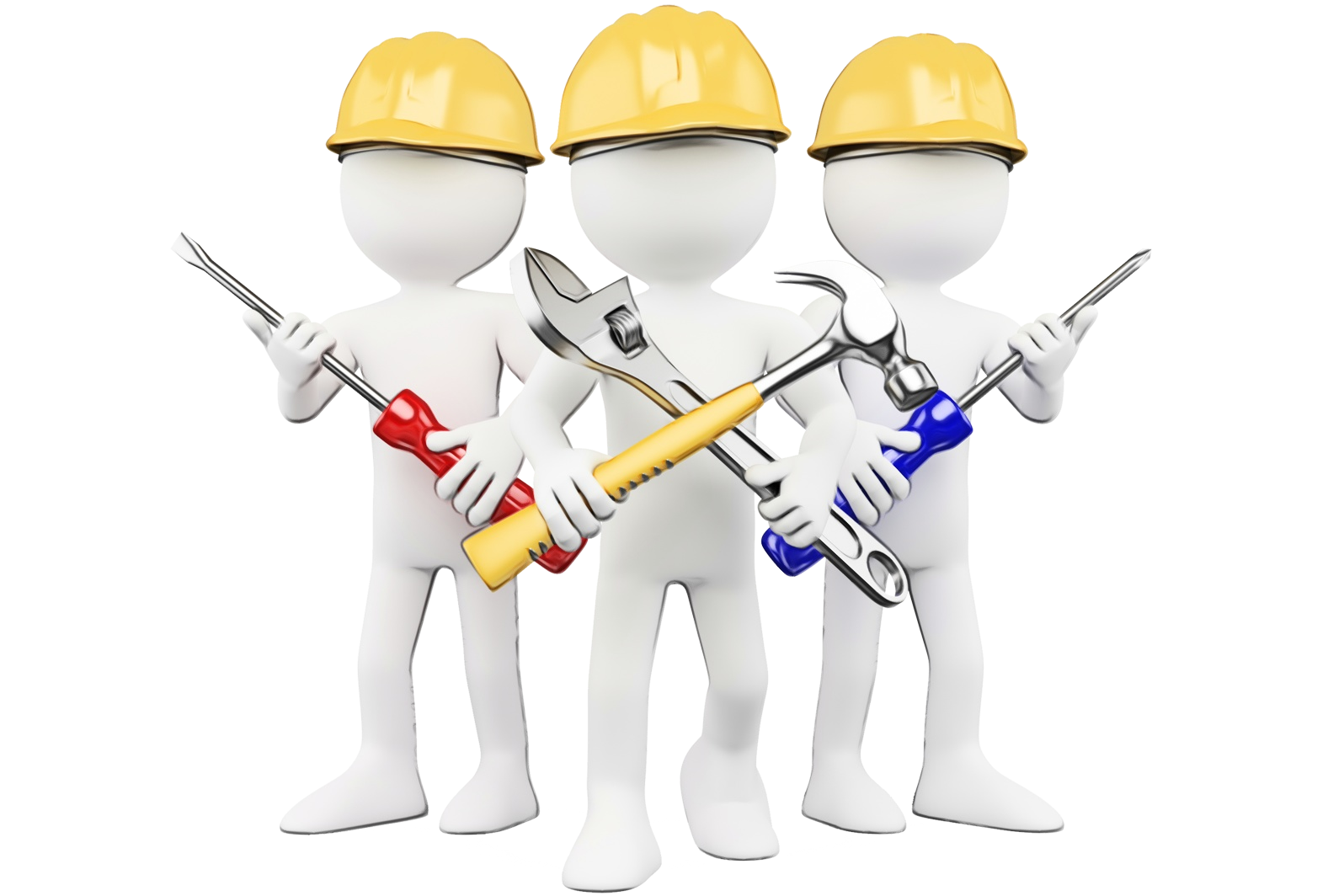
Hlavnou ideou uvedeného princípu je zabezpečenie čo možno najvyššej efektivity / dostupnosti zariadení a ľudí. Vznikol ako predpoklad fungovania princípu "JUST IN TIME".
Ak chceme TPM implementovať a pracovať na základe tohoto princípu je dôležité, aby boli splnené tieto hlavné podmienky:
- aktivita musí vychádzať od manažmentu - tím pracovníkov musí vidieť, že manažment spoločnosti bude túto aktivitu podporovať.
- do riešenia musí byť zapojený komplexný tím - výrobný pracovníci, výrobný lídri, pracovníci údržby, lídri z oddelenia údržby, technológia, pracovníci kvality a v neposlednom rade vrcholový manažment.
Medzi hlavné zásady TPM patrí:
- Nulové neplánované prestoje strojov.
- Nulové poruchy na zariadeniach spôsobené stavom stroja.
- Nulové straty na spomaľovaní taktu stroja.
"TPM je séria metód na zaistenie toho, že všetky stroje vo výrobnom procese sú k dispozícii v trvaní, aké je nevyhnutné na splnenie naplánovaných úloh a zabezpečia , že výroba nebude nikdy prerušená"
Zdroj: Jamesa Womak a Daniel T. Jones - "The machine change the world" , alebo "Stroje ktoré zmenia svet".
TPM má sedem hlavných krokov:
1. Začiatok čistenia
2. Odstránenie zdrojov z nečistenia
3. Štandardy pre čistenie
4. Všeobecná kontrola
5. Autonómna kontrola
6. Organizácia a poriadok
7. Rozvoj autonómnej údržby
Medzi základné metódy, ktorými vieme pracovať pomocou princípu TPM je:
- JIDOKA
- ANDON
- 5S
- Štandardizácia